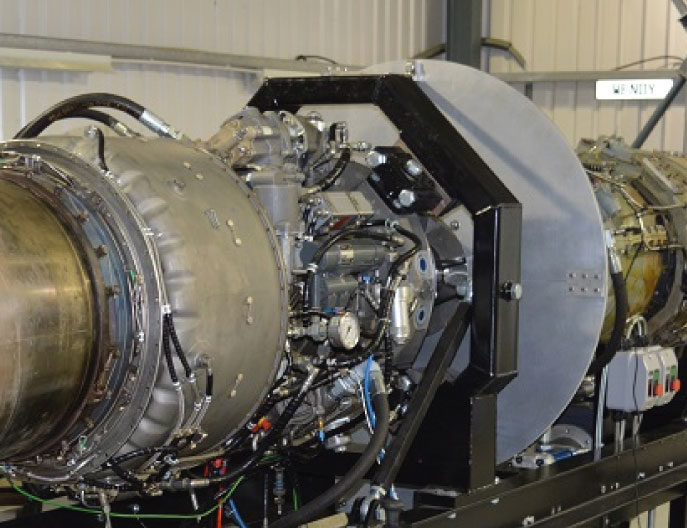
S&C Thermofluids - Stobart Division
[vc_row][vc_column][vc_empty_space height=”60px”][vc_column_text]
From the aerodynamics of a supersonic aircraft to the suction of a vacuum cleaner, the flow and heat transfer of the working fluid (thermofluids) determines the function and performance of such systems. Founded in 1987, S & C Thermofluids uses a full range of engineering tools to study and develop such systems.
The ability to construct prototypes and test pieces to demonstrate and validate systems is a key part of what S & C do. The experimental facilities and the items that are tested using them are constructed by the Stobart Division in Redruth, Cornwall.
When one of the engineers stumbled upon a video on You Tube of a Swift-Cut plasma cutting table in action, they knew straight away that they wanted their own. They chose the Swift-Cut 2500 for their very small workshop, impressed with its footprint and movability. The only space they had for it was on a mezzanine level, but fortunately Swift-Cut tables have forklift holes and so it was not a problem when it came to positioning it.
In the past, making research equipment has either meant outsourcing or using their handheld plasma cutter. The first was time consuming and limited the amount of work they could take on. The second was often inaccurate and messy and not capable of producing some of the designs that needed cutting. Indeed, Matthew Stobart of Stobart Division said, ‘we had a good quality hand plasma cutter for nearly twenty years, although this has been a useful tool it is amazing how different the Swift-Cut machine is. The cutting is predictable, accurate and amazingly clean with the water table, almost no fuss or mess.’
Matthew is quick to praise what having the table has meant for his business. He claims the table has changed the way they can now work. ‘The Swift-Cut table has revolutionised the way we do things, most of our work is one-off research equipment on a very fast turnaround so waiting for profiling companies to deliver parts was a big problem. Now we can cut profiles while the project is in the design stage and make changes in real time.’
In fact, Matthew said they have taken on two or three jobs in the last month alone which would not have been feasible without their own plasma table. One such job was sensitive and couldn’t be outsourced to a third party, so without the table they would have had to turn it down. With these jobs alone, Matthew is confident that the investment has paid off and indeed, that the table has already paid for itself.
Training took half a day and Matthew said all the staff can make use of the plasma cutting table, in fact now the engineers are so adept at using the machine that they are finding new ways to work with it all the time. As Swift-Cut prides itself on its innovation, they are thrilled that their clients are exceeding their expectations and utilising the scope of the machine to maximise its potential.
Indeed, Matthew says the technical abilities of the table and software almost seem limitless. Take double curvature work for example. In Matthews words, ‘When undertaking double curvature sheet metalwork it is difficult to arrive at the shape of the sheet you are going to start from and I am not aware of any computer software that allows you to predict this, because of the way the finished article is stretched/shrunk in multiple planes from the original sheet. Whereas for a developable shape like a tube or a box there is plenty of software that allows you to accurately work this out.
What we do is generate a pattern or buck usually by taking sections through the 3D model and cutting them out with the plasma table so that they interlock like a jigsaw puzzle, then weld and dress them into a pattern skeleton. Usually (using wide masking tape) we would then cover the section of the pattern we want to make, remove this as a single piece and lay it onto a flat surface, take a digital photo of it and put it our CAD package, generating a .DXF profile by tracing round it ensuring we have corrected for any aspect ratio scaling issues from the photo. Then we just pump this into the plasma cutter and minutes later you have your starting shape. This is not an exact science but it is far better than anything we did before.’
What Matthew says he finds as impressive as the technical abilities of the table is the after-care from Swift-Cut. He admits that having had the machine over a year he didn’t expect to get the help he still receives from the team when he needs some advice or assistance. However, if he ever needs support, he knows he can get on the phone and Swift-Cut will be happy to help.
Hearing Matthew talk about their plasma table, one thing is abundantly clear; the addition of the Swift-Cut 2500 plasma table to their workshop has had nothing but a positive impact on their business and moving forward, it will continue to allow them to surpass their expectations time and time again.
[/vc_column_text][/vc_column][/vc_row]