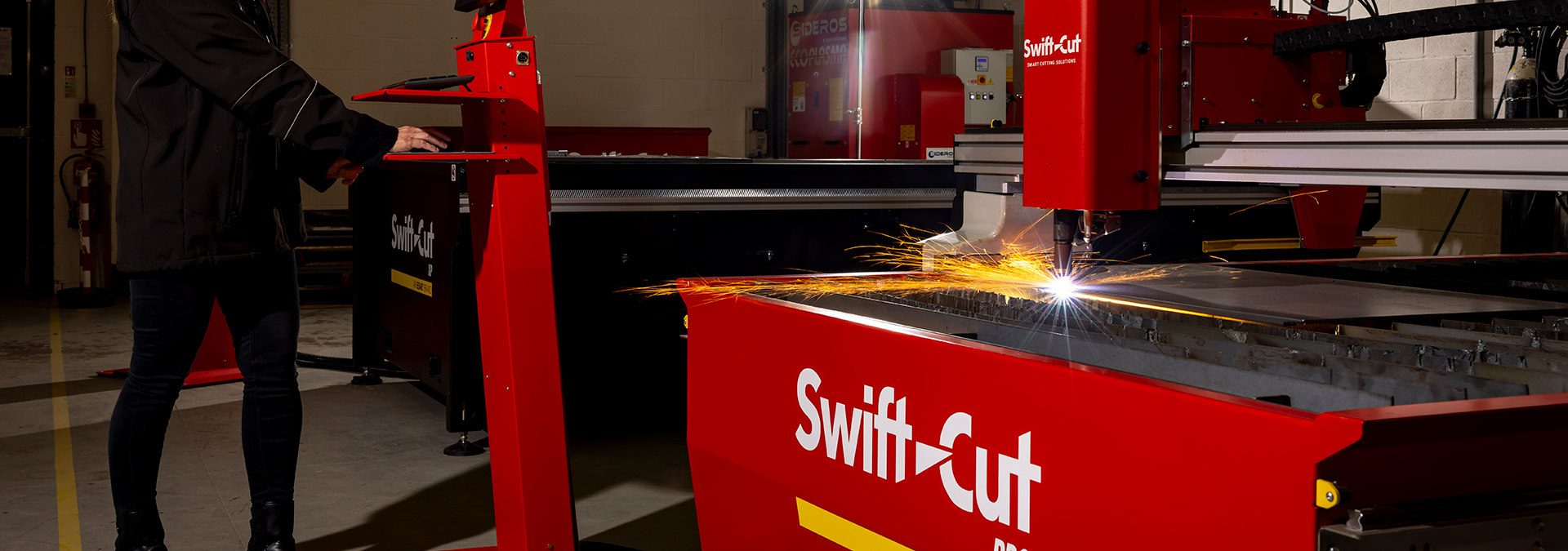
The Ultimate Guide to Choosing the Perfect CNC Plasma Table for Your Business
Factors to Consider When Choosing a CNC Plasma Table
A CNC plasma table offers precision, speed, versatility, and cost-effectiveness, with key components like the cutting bed, plasma torch, and CNC controller ensuring top performance. Choosing the right table depends on factors such as size, material thickness, software compatibility, and durability.
If you’re in the market for a CNC plasma table, you’ve likely encountered a range of options promising precision, efficiency, and durability. This guide will help you understand what a CNC plasma cutter table is, why it’s a game-changer in metal fabrication, and how to choose the perfect table for your operations.
What is a CNC Plasma Table?
A CNC plasma table is a computer-controlled cutting machine that uses a plasma torch to cut through materials like steel, aluminium, and other metals. “CNC” stands for “Computer Numerical Control,” meaning the machine follows programmed instructions to perform highly accurate cuts. These tables are ideal for industries like manufacturing, automotive repair, and construction, where precision and efficiency are critical.
The CNC plasma cutter table is the foundation of the setup, housing the plasma cutting mechanism and providing the stability and support needed to produce clean, precise cuts.
Key Benefits of a CNC Plasma Table
Precision and Accuracy
A CNC plasma table offers unmatched cutting accuracy compared to manual methods. The integration of computer control ensures each cut is made to exact specifications, reducing waste and improving product quality.
Speed and Efficiency
Using a CNC plasma cutter table significantly speeds up the cutting process. With advanced programming, the machine can handle complex designs and cut through thick materials in a fraction of the time it would take manually.
Versatility
Whether you’re cutting intricate designs or slicing through heavy-duty steel, a CNC plasma table can handle a variety of materials and thicknesses, making it a versatile tool for various applications.
Cost-Effectiveness
While the initial investment in a CNC plasma table might seem significant, the long-term savings in labour, material waste, and production time make it a cost-effective solution.
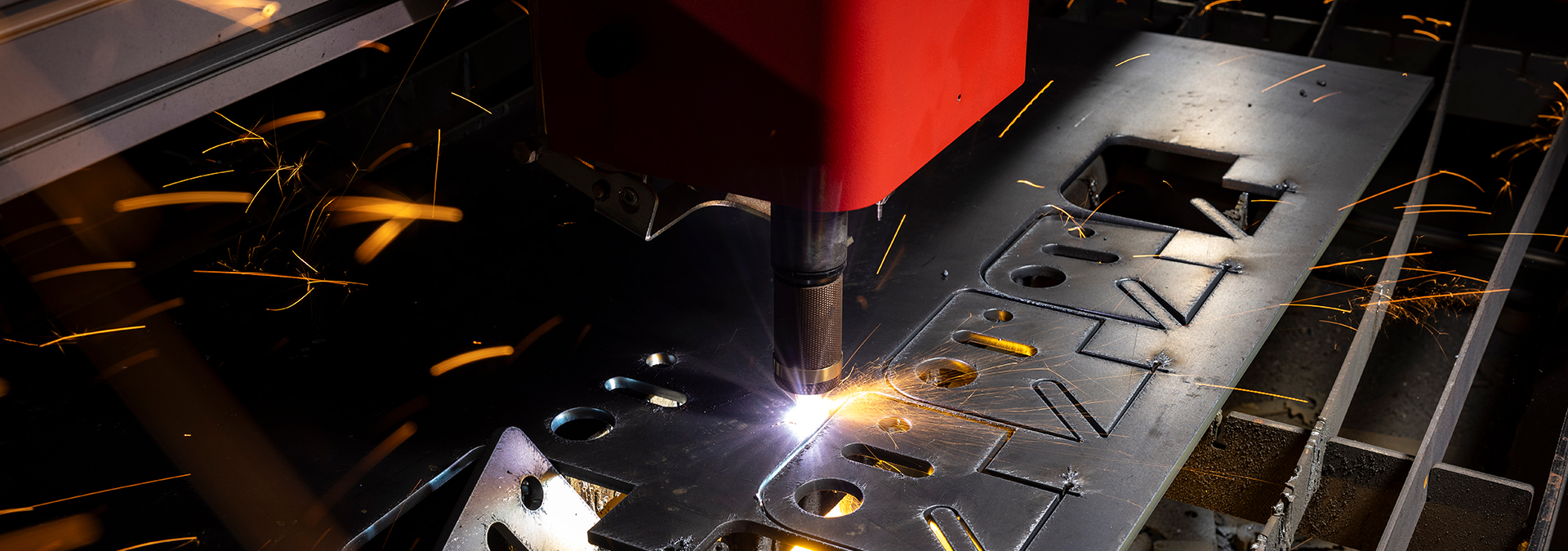
Components of a CNC Plasma Table
Understanding the key components of a CNC plasma cutter table will help you make an informed decision when purchasing:
The Cutting Bed
The cutting bed is the flat surface where materials are placed during cutting. Look for a table with a durable and corrosion-resistant bed to withstand heavy use.
Plasma Torch
The plasma torch generates the plasma arc that cuts through the material. Modern plasma torches offer increased precision and longer lifespans.
CNC Controller
The CNC controller is the brain of the operation. It executes the programmed instructions and directs the plasma cutter. Advanced controllers provide features like touchscreens and easy-to-use interfaces.
Drive System
The drive system moves the torch along the X, Y, and sometimes Z axes. A high-quality drive system ensures smooth and precise movements.
Ventilation or Water Table
Proper ventilation or a water table is essential for managing fumes and debris generated during cutting, ensuring a safe working environment.
Factors to Consider When Choosing a CNC Plasma Table
Table Size
The size of the CNC plasma table determines the maximum dimensions of the material you can work with. For large-scale industrial operations, a table with a bigger cutting area is ideal. Smaller shops might prefer compact tables.
Material Thickness
Consider the thickness of the materials you’ll be cutting. Ensure the CNC plasma cutter table you choose is powerful enough to handle the maximum thickness required.
Software Compatibility
Check whether the table is compatible with popular CAD and CAM software, as this will simplify the design and programming process.
Durability and Build Quality
Invest in a table made from high-quality materials to ensure longevity and consistent performance.
Budget
While it might be tempting to choose the most affordable option, prioritise quality and features over cost. A reliable CNC plasma cutter table is an investment that will pay off in the long run.
After-Sales Support
Choose a manufacturer that offers excellent customer support, including training, maintenance, and access to spare parts.
Popular Applications of CNC Plasma Tables
A CNC plasma table is a versatile tool that caters to a wide range of industries:
Metal Fabrication
From custom brackets to decorative panels, a CNC plasma cutter table can handle detailed designs with ease.
Automotive
The automotive industry relies on plasma tables for creating precise components, such as chassis parts and exhaust systems.
Sign Making
Sign makers use CNC plasma tables to cut intricate designs from metal sheets, creating eye-catching signage.
Construction
Plasma tables are used to cut structural components for buildings, ensuring accurate dimensions and faster assembly.
Art and Design
Artists and designers leverage the precision of CNC plasma cutter tables to create stunning metal art and sculptures.
The Swift-Cut Advantage
Swift-Cut is a leading manufacturer of CNC plasma tables, renowned for its innovative designs and user-friendly features. Here’s why Swift-Cut stands out:
Wide Range of Options
Swift-Cut offers a variety of CNC plasma cutter tables, catering to different budgets and requirements.
State-of-the-Art Technology
With advanced features like touchscreens, intuitive software, and high-precision components, Swift-Cut tables are designed for optimal performance.
Robust Build Quality
Swift-Cut tables are built to last, with durable materials and a design that minimizes wear and tear.
Customer Support
Swift-Cut provides exceptional after-sales support, including training, troubleshooting, and access to spare parts.
Maintaining Your CNC Plasma Table
Proper maintenance of your CNC plasma table is essential to ensure consistent performance, accuracy, and longevity. Regular upkeep not only maximises efficiency but also prevents costly downtime due to avoidable repairs. Below is a detailed guide on the most critical maintenance tasks to keep your CNC plasma cutter table in peak condition.
- Clean the Cutting Bed
The cutting bed is the workspace where materials are secured during the cutting process. Over time, debris, slag, and remnants of metal can accumulate on the surface.
- Why it matters: A dirty cutting bed can interfere with material placement, leading to inaccuracies in cuts. Debris can also damage the table’s surface or obstruct the cutting process.
- How to clean:
- After every use, remove loose debris using a brush or scraper.
- Periodically, use a vacuum or compressed air to clean hard-to-reach areas.
- For water tables, drain and replace the water regularly to prevent sludge buildup.
- Pro Tip: Consider applying a rust inhibitor to the bed, especially if it is exposed to moisture.
- Inspect the Plasma Torch
The plasma torch is the heart of your CNC plasma cutter table, responsible for generating the plasma arc that cuts through the material. Frequent use can lead to wear on consumable parts, such as electrodes and nozzles.
- Why it matters: A worn or damaged torch can cause irregular cuts, reduced precision, and increased material wastage.
- How to inspect:
- Regularly check the condition of the nozzle and electrode for wear or damage.
- Look for signs of irregular arc formation, such as uneven cuts or excessive dross.
- Replace consumables as soon as they reach their wear limits to prevent further damage.
- Pro tip: Keep a stock of replacement consumables on hand to minimise downtime.
- Lubricate moving parts
The drive system and other moving components of a CNC plasma table are essential for smooth and precise operation. Over time, these parts can experience wear and tear due to friction.
- Why it matters: Proper lubrication reduces friction, prevents overheating, and extends the life of moving parts. It also ensures smooth, accurate motion along the X, Y, and Z axes.
- How to lubricate:
- Use a high-quality lubricant recommended by the table manufacturer.
- Focus on linear guides, bearings, and drive mechanisms.
- Avoid over-lubricating, as this can attract dust and debris.
- Pro tip: Develop a schedule for lubrication based on the frequency and intensity of use.
- Update Software
The CNC controller is the brain of your CNC plasma cutter table, and its software must remain up to date to ensure optimal performance.
- Why it matters: Updates often include bug fixes, new features, and compatibility improvements with the latest design software. Outdated software can lead to programming errors or reduced efficiency.
- How to update:
- Regularly check the manufacturer’s website for software updates.
- Follow the recommended procedure for downloading and installing updates.
- Back up your settings and programs before performing updates to avoid data loss.
- Pro tip: Train your team to recognise and troubleshoot common software-related issues.
- Check Ventilation or Water Table System
A CNC plasma table generates heat, fumes, and debris during cutting. Managing these byproducts is crucial for maintaining a safe and efficient working environment.
- Why it matters: Proper ventilation or a well-maintained water table helps reduce airborne particles, minimises health hazards, and prevents equipment damage from heat and debris.
- How to maintain ventilation:
- Inspect ductwork and fans for clogs or damage.
- Replace filters regularly to ensure optimal airflow.
- How to maintain a water table:
- Ensure the water level is appropriate to capture sparks and debris.
- Periodically clean the water table to remove accumulated sludge.
- Pro tip: Consider using additives in your water table to prevent rust and bacteria growth.
Additional Maintenance Tips
Perform regular inspections
- Schedule routine inspections to identify potential issues before they escalate.
- Create a checklist of components to review, including electrical connections, belts, and fasteners.
Train Your Operators
- Ensure operators understand the maintenance requirements of the machine.
- Provide training on proper cleaning, lubrication, and troubleshooting techniques.
Keep Spare Parts on Hand
- Maintain an inventory of commonly replaced parts, such as consumables, filters, and belts, to reduce downtime.
Calibrate Periodically
- Periodic calibration ensures the machine maintains cutting accuracy.
- Follow the manufacturer’s guidelines for recalibration frequency.
Record Maintenance Activities
- Keep a log of maintenance activities, including dates, tasks performed, and any replacement parts used.
- Use this log to identify patterns and optimise maintenance schedules
Benefits of Regular Maintenance
- Enhanced Performance: A well-maintained CNC plasma table operates at peak efficiency, producing high-quality cuts every time.
- Longer Lifespan: Proper care extends the life of your machine, maximizing your investment.
- Reduced Downtime: Preventative maintenance minimises unexpected breakdowns, ensuring uninterrupted production.
- Safety: Clean and well-maintained equipment reduces the risk of accidents and exposure to harmful fumes.
By following these detailed maintenance practices, you can ensure that your CNC plasma cutter table delivers consistent, high-quality results and remains a reliable tool in your production process. Investing time in maintenance now will save you time, money, and hassle in the long run.
FAQs About CNC Plasma Tables
Q: What materials can a CNC plasma cutter table handle?
A: CNC plasma tables can cut various metals, including steel, aluminium, copper, and brass. Some tables can even handle non-metallic materials.
Q: Is a CNC plasma table suitable for beginners?
A: Many CNC plasma tables, including Swift-Cut models, are designed with user-friendly features, making them suitable for beginners with proper training.
Q: How much does a CNC plasma table cost?
A: The cost of a CNC plasma table varies based on size, features, and build quality. It is best to choose a company that will listen to your needs and quote accordingly, rather than sell you extras you do not need.
Q: Why is safety important when using metalworking fluids with a CNC plasma table?
A: Metalworking fluids help cool and lubricate materials during cutting, but improper handling or exposure can pose health risks, such as skin irritation or respiratory issues. Understanding and following safety protocols ensures a safer and more efficient working environment. For detailed guidelines, refer to OSHA’s Metalworking Fluids Manual.
Q: Can a CNC plasma table cut 3D shapes?
A: Some advanced CNC plasma cutter tables include multi-axis capabilities, allowing for 3D cutting.
Q: How do I choose between a water table and a downdraft table?
A: Water tables are ideal for managing sparks and dust, while downdraft tables are better for removing fumes in certain setups.
Investing in a CNC plasma table is a smart decision for anyone in the metal fabrication industry. With its precision, efficiency, and versatility, a CNC plasma cutter table can revolutionize your production process. By considering factors like table size, material thickness, and software compatibility, you can find the perfect table to meet your needs.
Swift-Cut’s range of CNC plasma tables combines cutting-edge technology with robust build quality, making it a top choice for professionals worldwide. Whether you’re a seasoned fabricator or a newcomer, a Swift-Cut CNC plasma cutter table is an investment that will elevate your capabilities and deliver exceptional results.
- Why is a CNC plasma cutting table faster than other methods?
CNC plasma cutting machines use a high-velocity jet of ionised gas (plasma) to melt and cut through metal efficiently. The computer-controlled system ensures precise movements, allowing the machine to cut complex patterns at high speeds without needing to slow down for accuracy. This makes it ideal for high-volume production. - What materials can a CNC plasma cutting table handle?
CNC plasma cutters are designed to cut conductive metals, including steel, stainless steel, aluminium, copper, and brass. Depending on the machine’s power and setup, they can handle various material thicknesses, from thin sheets to heavy-duty metal plates, making them versatile for a wide range of applications. - Is a CNC plasma cutting table affordable?
While the initial investment in a CNC plasma cutter can be significant, it is generally more affordable than laser cutting machines, especially for businesses that don’t require ultra-fine precision. The long-term cost savings from reduced material waste, faster production, and lower maintenance make it a cost-effective solution for many operations. - How accurate is a CNC plasma cutter?
CNC plasma cutters offer high precision, delivering clean, smooth cuts with minimal dross (slag). While not as precise as laser cutters for extremely intricate details, they are more than sufficient for most industrial applications, producing high-quality results that often require little to no post-processing. - I’ve never used a CNC plasma cutting machine, can I operate it?
Yes, modern CNC plasma cutters are designed with user-friendly interfaces and intuitive software. Many models feature touchscreens, step-by-step guides, and pre-set cutting parameters, making it easy for beginners to start using the machine with minimal training. This accessibility reduces the learning curve and allows new operators to produce high-quality cuts quickly. - What maintenance does a CNC plasma cutter need?
Regular maintenance includes cleaning the cutting bed to remove debris, inspecting the torch for wear, replacing consumables like electrodes and nozzles, lubricating moving parts to prevent friction, and updating software to access the latest features. Proper ventilation or water table management is also crucial for maintaining a safe and efficient work environment. - How does a CNC plasma cutter compare to a laser cutter?
CNC plasma cutters are faster and more affordable than laser cutters, making them ideal for general-purpose metal cutting. While laser cutters are more precise for intricate designs and can handle non-conductive materials, plasma cutters excel in cutting thick, conductive metals efficiently. They are the preferred choice for industries prioritising speed and cost-effectiveness. - What industries use CNC plasma cutting machines?
CNC plasma cutters are widely used in industries such as metal fabrication (for custom parts and structural components), automotive (for chassis and exhaust systems), construction (for beams and metal frameworks), and signage (for intricate designs in metal signs). They are also popular among artists creating metal sculptures and decorative pieces. - Can a CNC plasma cutter handle thick materials?
Yes, CNC plasma cutters are well-suited for cutting thick metal plates, with some models capable of cutting through steel over an inch thick. The machine’s power determines the maximum thickness it can handle, and higher-power machines are specifically designed for heavy-duty applications in industrial settings. - What software works with CNC plasma machines?
CNC plasma cutters are compatible with CAD (Computer-Aided Design) and CAM (Computer-Aided Manufacturing) software. Popular options include AutoCAD, SolidWorks, and Fusion 360, which allow users to create detailed designs and translate them into machine-readable cutting instructions. This integration streamlines the workflow, from design to production, ensuring precision and efficiency.