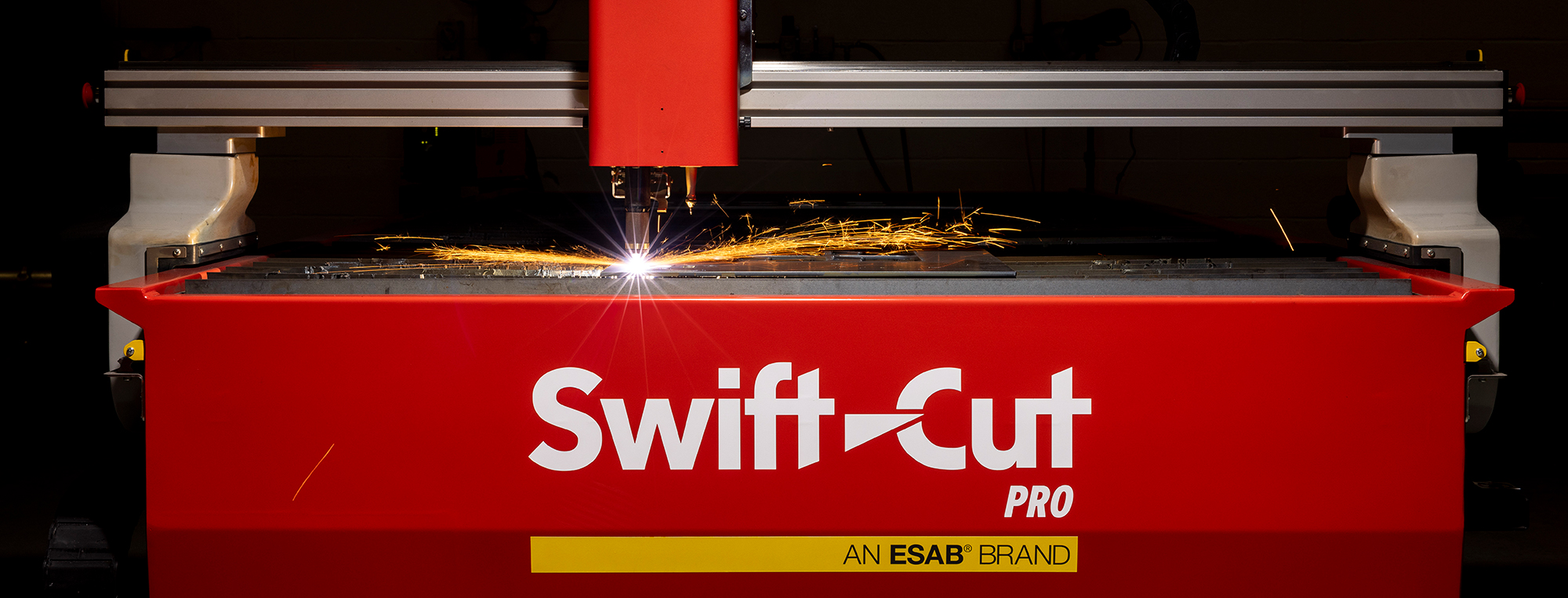
Revolutionise precision cutting with CNC plasma technology
What Is CNC Plasma and How Does It Work?
The Key Benefits of Using a CNC Plasma Cutter
Top Applications of CNC Plasma Cutting Across Industries
How to Choose the Perfect CNC Plasma Cutter for Your Needs
Maintenance Tips to Maximize the Life of Your CNC Plasma Machine
Why Swift-Cut Is the Ultimate Choice for CNC Plasma Solutions
What You’ll Learn About CNC Plasma Cutting
This comprehensive guide dives into everything you need to know about CNC plasma cutting – from how it works to its incredible precision, versatility, and cost-effectiveness. Whether you’re in metal fabrication, automotive, or industrial manufacturing, explore how a CNC plasma cutter can revolutionise your workflow and deliver unmatched results.
CNC Plasma: Transforming the Future of Precision Cutting
CNC plasma technology has revolutionised industries requiring precision cutting by offering unparalleled speed, accuracy, and efficiency. From automotive manufacturing to custom metal fabrication, a CNC plasma cutter is an indispensable tool for businesses aiming to enhance productivity while maintaining the highest quality standards. In this comprehensive guide, we’ll explore the capabilities, benefits, and applications of CNC plasma cutting, shedding light on why it’s a must-have for modern workshops.
What Is CNC Plasma?
Plasma cutter CNC combines computer numerical control (CNC) with plasma cutting technology to create a highly accurate and automated cutting process. Plasma cutting itself involves using a jet of hot plasma to cut through electrically conductive materials, such as steel, stainless steel, and aluminium.
The integration of CNC technology allows for precise control over the plasma cutter, enabling intricate shapes, designs, and cuts that are difficult or impossible to achieve manually. A plasma CNC machine is programmed to follow specific designs, ensuring repeatability and consistency across projects.
How Does a CNC Plasma Cutter Work?
The operation of a CNC plasma cutter can be broken down into several key steps:
- Programming the Design
Using CAD (Computer-Aided Design) software, users create a digital blueprint of the desired cut. This design is converted into G-code, which the CNC system interprets. - Material Setup
The workpiece is placed on the machine bed, often supported by a grid or slats to allow the plasma jet to penetrate fully. - Plasma Arc Generation
The plasma cutter generates an electric arc that ionizes gas, creating plasma. This plasma is then directed at the material to melt and blow away the unwanted sections. - Precision Cutting
Guided by the CNC system, the plasma cutter follows the programmed path with exceptional accuracy, producing clean and precise cuts. - Finishing Touches
Post-cutting, minor refinements such as deburring or sanding may be needed to achieve the final finish.
Key Benefits of CNC Plasma Cutting
Adopting CNC plasma cutting in your workshop or production facility offers a multitude of advantages:
Unmatched Precision
CNC technology ensures that each cut is executed with pinpoint accuracy, allowing for intricate designs and tight tolerances.
High Speed
Compared to traditional cutting methods, a plasma CNC system operates significantly faster, reducing production times and increasing output.
Versatility
A CNC plasma cutter can handle various materials and thicknesses, from thin sheets of aluminium to thick steel plates.
Cost-Effective
The automation and efficiency of CNC plasma cutting reduce labour costs and material waste, delivering a higher ROI.
Repeatability
Once programmed, a CNC plasma machine can replicate the same cut repeatedly with no loss in quality.
Ease of Use
Modern plasma CNC machines feature user-friendly interfaces, making them accessible to both experienced technicians and beginners.
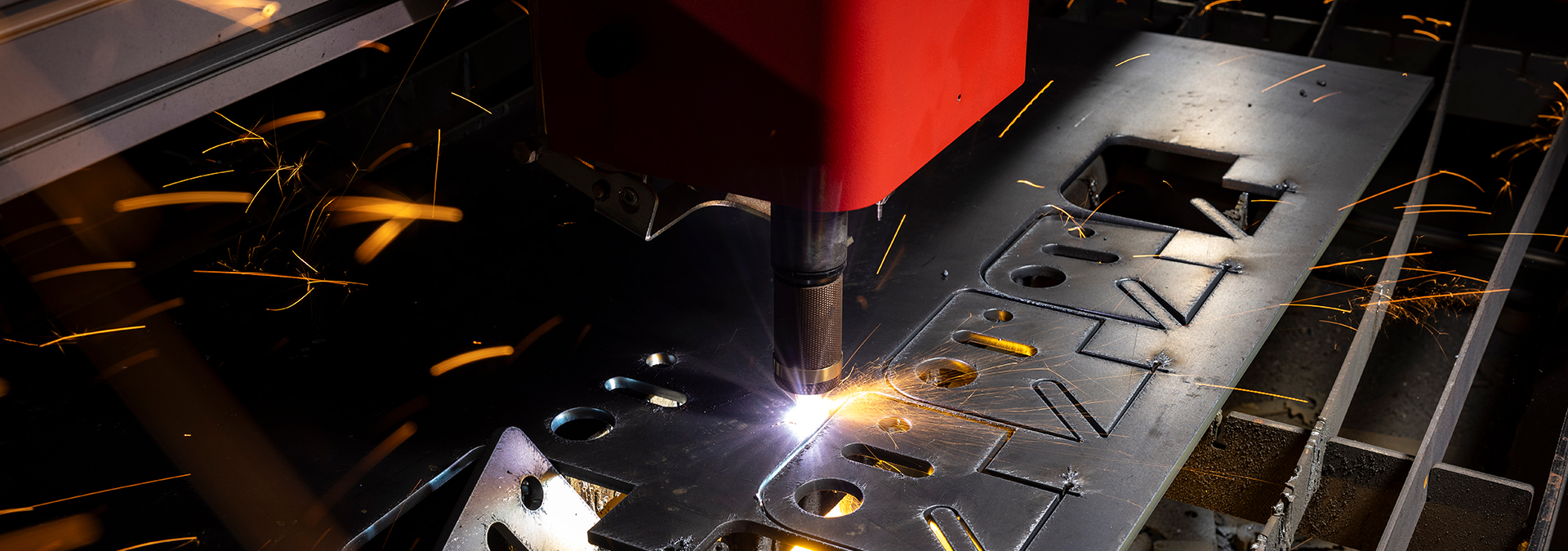
Applications of CNC Plasma Cutting
The versatility of CNC plasma cutting makes it ideal for a wide range of industries and applications:
Metal Fabrication
From creating brackets and enclosures to decorative panels, CNC plasma cutting is a staple in custom metalwork.
Automotive and Aerospace
The precision and consistency of CNC plasma cutters are critical in crafting components for vehicles and aircraft.
Construction and Architecture
Plasma cutters produce structural components, railings, and custom signage with ease and accuracy.
Industrial Manufacturing
High-volume production of machine parts and equipment components relies on the efficiency of CNC plasma systems.
Art and Design
Artists and designers use CNC plasma cutting to bring intricate metal creations to life, from sculptures to furniture.
Selecting the ideal plasma CNC machine for your needs depends on several factors:
Material Types and Thicknesses
Ensure the cutter can handle the materials you work with most frequently, whether it’s thin aluminium or thick steel.
Table Size and Cutting Area
Consider the maximum sheet size you’ll need to cut and choose a machine with an appropriately sized table.
Cutting Speed
Evaluate the machine’s cutting speed to ensure it meets your production requirements.
Software Compatibility
Look for a system compatible with popular CAD/CAM software for seamless integration.
Cost and ROI
While upfront costs can vary, consider the long-term savings and productivity boosts a CNC plasma cutting machine offers.
Maintenance Tips for CNC Plasma Cutters
To ensure the longevity and performance of your CNC plasma cutting system, follow these maintenance best practices:
- Regularly Inspect Consumables: Replace worn nozzles, electrodes, and shields to maintain cutting quality.
- Keep the Machine Clean: Remove debris and dust from the table and cutting head after each use.
- Monitor Gas and Air Pressure: Consistent gas and air pressure are crucial for optimal plasma generation.
- Check Software Updates: Keep your CNC system software up to date to leverage the latest features and improvements.
Why Swift-Cut Is the Leader in CNC Plasma Cutting
Swift-Cut stands out as a trusted name in CNC plasma cutting technology. With a commitment to innovation, precision, and customer support, Swift-Cut offers cutting-edge plasma CNC machines tailored to various industries and applications. Whether you’re a small business or a large manufacturer, Swift-Cut provides the tools you need to stay competitive.
Swift-Cut’s machines are designed for ease of use, reliability, and exceptional cutting quality, ensuring that every project meets your exact specifications. With a range of table sizes and cutting capacities, Swift-Cut has a solution for every workshop.
Elevate Your Cutting Game with CNC Plasma
Investing in a CNC plasma cutter is more than just upgrading your equipment—it’s a step toward enhanced efficiency, precision, and profitability. From reducing waste to enabling intricate designs, CNC plasma technology transforms the way businesses approach cutting tasks.
For those seeking the best in CNC plasma cutting, Swift-Cut offers unparalleled solutions that combine innovation, reliability, and support. Explore Swift-Cut’s range of plasma CNC machines today and discover how they can revolutionise your workshop.
- What is CNC plasma cutting, and how does it work?
CNC plasma cutting uses a computer-controlled torch to cut materials by directing a high-temperature plasma jet through conductive metals like steel, aluminium, and copper. The precision of CNC technology ensures accurate and efficient cutting. - What are the main benefits of using a CNC plasma cutter in manufacturing?
CNC plasma cutters offer speed, precision, versatility, reduced material waste, and the ability to handle complex designs, making them invaluable for improving manufacturing efficiency.
- Which industries commonly use CNC plasma cutting, and why?
Industries such as automotive, metal fabrication, aerospace, construction, and HVAC use CNC plasma cutters for their ability to deliver fast, accurate, and cost-effective results across various projects.
- How does CNC plasma compare to other cutting technologies?
CNC plasma cutting is faster and more cost-effective than laser cutting for thick metals and provides cleaner cuts compared to oxy-fuel methods, making it ideal for heavy-duty applications. - What should I consider when choosing a CNC plasma machine?
Consider factors like material thickness, cutting speed, table size, power source, software compatibility, and budget. Swift-Cut experts can guide you to the right machine for your needs.
- What materials can be cut using a CNC plasma cutter?
CNC plasma cutters can cut conductive metals such as steel, stainless steel, aluminium, brass, and copper, with varying thickness capabilities depending on the machine.
- What are the maintenance requirements for a CNC plasma cutter?
Routine maintenance includes inspecting and replacing consumables, cleaning the torch and cutting table, checking cables and hoses, and keeping software updated for optimal performance.
- How can CNC plasma cutting improve efficiency in production?
CNC plasma cutting reduces production time by delivering fast, precise cuts, minimizes waste with accurate programming, and lowers labour costs by automating complex cutting tasks. - What types of projects are best suited for CNC plasma cutting?
CNC plasma cutting excels in projects requiring fast, accurate cuts on metals, such as industrial parts, custom signage, automotive components, and construction materials.