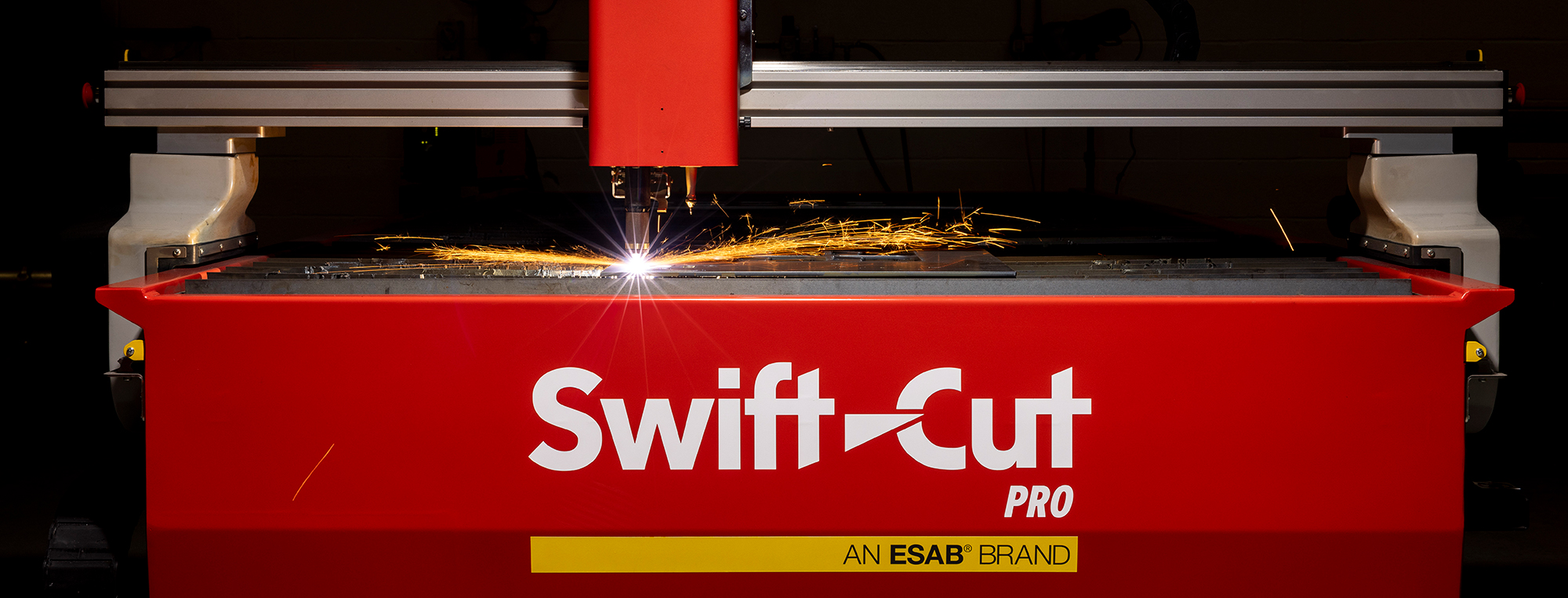
Achieving Precision: A Complete Guide to CNC Plasma Cutter Tolerances
Factors Influencing CNC Plasma Cutter Tolerances
CNC plasma cutter tolerances are influenced by various factors, including machine quality, material type and thickness, cutting speed, plasma gas settings, and operator expertise, all of which play a crucial role in determining precision and performance.
The No 1 Essential Guide to CNC Plasma Cutter Tolerances
When precision meets performance in metal fabrication, one tool often stands out: the CNC plasma cutter. A vital factor determining its efficacy is tolerance—the level of accuracy a machine achieves in cutting materials. For businesses relying on precision in industries like automotive, aerospace, and industrial manufacturing, understanding CNC plasma cutter tolerances is essential to ensure quality and efficiency.
This comprehensive guide explores everything you need to know about CNC plasma cutter tolerances, including factors influencing accuracy, how to optimise performance, and why tolerances matter for your bottom line.
What Are CNC Plasma Cutter Tolerances?
Tolerance refers to the allowable deviation from the specified dimensions of a cut. For example, if your design requires a part to be 100mm, a machine with a tolerance of ±0.5mm can produce cuts between 99.5mm and 100.5mm. In CNC plasma cutting, tighter tolerances equate to higher precision but may also increase costs and processing time.
Factors Influencing CNC Plasma Cutter Tolerances
Achieving precise cuts with a CNC plasma cutter depends on several variables:
- Machine Type and Build Quality
High-quality CNC plasma cutters are engineered with precision components that enable tighter tolerances. Machines with robust frames, advanced motion systems, and high-resolution controls deliver more consistent results. - Torch Design
The type and quality of the plasma torch impact accuracy. High-definition plasma systems are designed for superior precision compared to standard systems, offering tighter tolerances. - Material Type and Thickness
Material Type: Softer metals like aluminium are easier to cut but may experience more warping, affecting tolerances. Harder materials like stainless steel generally allow for better edge accuracy.
Thickness: Thinner materials are more susceptible to heat distortion, which can affect the precision of the cut. - Cutting Speed
Faster cutting speeds can reduce the quality of cuts, leading to rougher edges and looser tolerances. Balancing speed with quality is essential for optimal results. - Plasma Gas and Settings
The type of gas used (e.g., oxygen, nitrogen, or air) and its flow rate can influence the quality of the cut. Incorrect settings can result in wider kerf widths, impacting tolerances. - Kerf Width
The kerf is the width of the material removed during cutting. Variations in kerf width can cause deviations from the desired dimensions, affecting overall accuracy. - Operator Skill
While CNC machines automate much of the process, operator expertise in setting up and maintaining the machine significantly impacts the final results.
Typical Tolerances for CNC Plasma Cutters
The tolerances achievable with a CNC plasma cutter vary significantly based on the machine’s capabilities, the application requirements, and the material being cut. Understanding these tolerances is crucial for ensuring that your cuts meet the necessary specifications for your project. Below is a detailed breakdown:
Standard Precision Plasma Cutting
For most general-purpose CNC plasma cutting systems, tolerances typically range between ±0.5mm and ±1mm. These machines are ideal for projects where high precision is not critical, such as cutting large structural components or fabricating parts with generous design clearances. Standard precision systems are cost-effective, fast, and versatile, making them a popular choice for many industries.
High-Definition Plasma Cutting
High-definition (HD) plasma systems offer significantly tighter tolerances, achieving accuracies as precise as ±0.25mm. These systems are equipped with advanced torch technology, refined motion controls, and optimized plasma gas settings to deliver clean, sharp edges with minimal dross. High-definition plasma is often used for applications where intricate designs, fine details, or exact fits are essential, such as in automotive manufacturing, aerospace engineering, and high-end architectural projects.
Impact of Material Thickness on Tolerances
Material thickness plays a critical role in the accuracy of plasma cuts. As thickness increases, so does the complexity of maintaining tight tolerances. Here’s how material thickness affects tolerances:
- Thin Materials (Up to 3mm):
Thin materials generally allow for tighter tolerances because they require less heat input, minimizing distortion. However, careful handling is still necessary to avoid issues like warping, especially in materials prone to heat sensitivity, such as aluminium. - Medium Thickness Materials (3mm to 25mm):
This range strikes a balance between precision and practicality. CNC plasma cutters excel in this category, offering consistent tolerances that meet the demands of most industrial and manufacturing applications. - Thick Materials (Over 25mm):
When cutting thicker materials, maintaining tight tolerances becomes more challenging. Increased heat input and a wider kerf can cause slight deviations, leading to tolerances that are slightly looser compared to thinner materials. High-definition systems can still achieve impressive accuracy, but results may vary based on the material type and cutting speed.
By selecting the right plasma cutting system and optimising the cutting process for your material and project requirements, you can achieve the desired balance between precision and efficiency, regardless of material thickness.
Comparing CNC Plasma Cutting with Other Methods
When deciding if a CNC plasma cutter is right for your operation, comparing tolerances with alternative cutting methods is helpful:
- Laser Cutting
Laser cutters achieve extremely tight tolerances, often within ±0.1mm. However, they are more expensive and less efficient for thicker materials.
- Waterjet Cutting
Waterjet systems can match or exceed plasma cutting tolerances, particularly for intricate designs. However, they have slower cutting speeds and higher operational costs.
- Oxy-Fuel Cutting
Suitable for thick materials, oxy-fuel cutting has significantly looser tolerances, often around ±1-2mm.
- CNC Plasma Cutting
Offers a balance of precision, speed, and cost, making it ideal for medium- to high-precision applications across a variety of materials.
Improving CNC Plasma Cutter Tolerances
To achieve optimal tolerances, follow these best practices:
- Regular Maintenance
Clean and inspect components such as the torch, nozzle, and electrode regularly to prevent performance degradation.
- Optimize Settings
Adjust cutting parameters like speed, amperage, and gas flow to suit the material and desired precision.
- Upgrade Components
Consider investing in a high-definition plasma system for tighter tolerances.
- Use Quality Consumables
Worn or low-quality consumables can lead to inconsistent cuts. Use manufacturer-recommended parts for the best results.
- Implement Proper Fixturing
Secure the material firmly to minimize vibrations and movement during cutting.
- Perform Test Cuts
Test cuts allow you to evaluate and fine-tune settings before starting full production.
Applications Where Tolerances Matter
CNC plasma cutter tolerances are critical in industries where precision directly impacts functionality and safety. Examples include:
- Automotive Manufacturing
Accurate parts are essential for vehicle assembly and performance, from brackets to chassis components.
- Aerospace Engineering
Stringent tolerances are mandatory to meet industry regulations and ensure safety in aircraft manufacturing.
- Architectural Fabrication
Decorative and structural components require tight tolerances to fit seamlessly into projects.
- Industrial Equipment
Accurate cuts ensure machinery parts meet functional requirements and reduce wear.
CNC Plasma Cutter Tolerances: Cost vs. Precision
Achieving tighter tolerances often comes with increased costs, driven by factors like slower cutting speeds, advanced systems, and high-quality consumables. To balance cost and precision:
- Define Tolerance Requirements:
Match tolerances to your project’s needs. Over-specifying tolerances can inflate costs unnecessarily. - Use High-Definition Systems Strategically:
Reserve high-definition plasma cutting for parts requiring extreme accuracy and standard systems for less demanding cuts. - Optimise Workflow:
Combining CNC plasma cutting with post-processing techniques like grinding can achieve desired tolerances more cost-effectively.
Future Trends in CNC Plasma Cutting Tolerances
Advancements in CNC plasma cutting technology are driving improved tolerances and expanding the applications of this versatile tool. Key trends include:
- Enhanced Automation
Integration with CAD/CAM software streamlines design-to-production workflows, reducing errors.
- AI-Driven Optimisation
AI algorithms can analyse cutting patterns and adjust parameters in real time for improved precision.
- Hybrid Systems
Combining plasma cutting with other technologies, like laser or waterjet, is becoming more common to achieve tighter tolerances in diverse applications.
- Eco-Friendly Solutions
Efforts to minimise waste and energy use in plasma cutting are paving the way for greener operations without compromising accuracy.
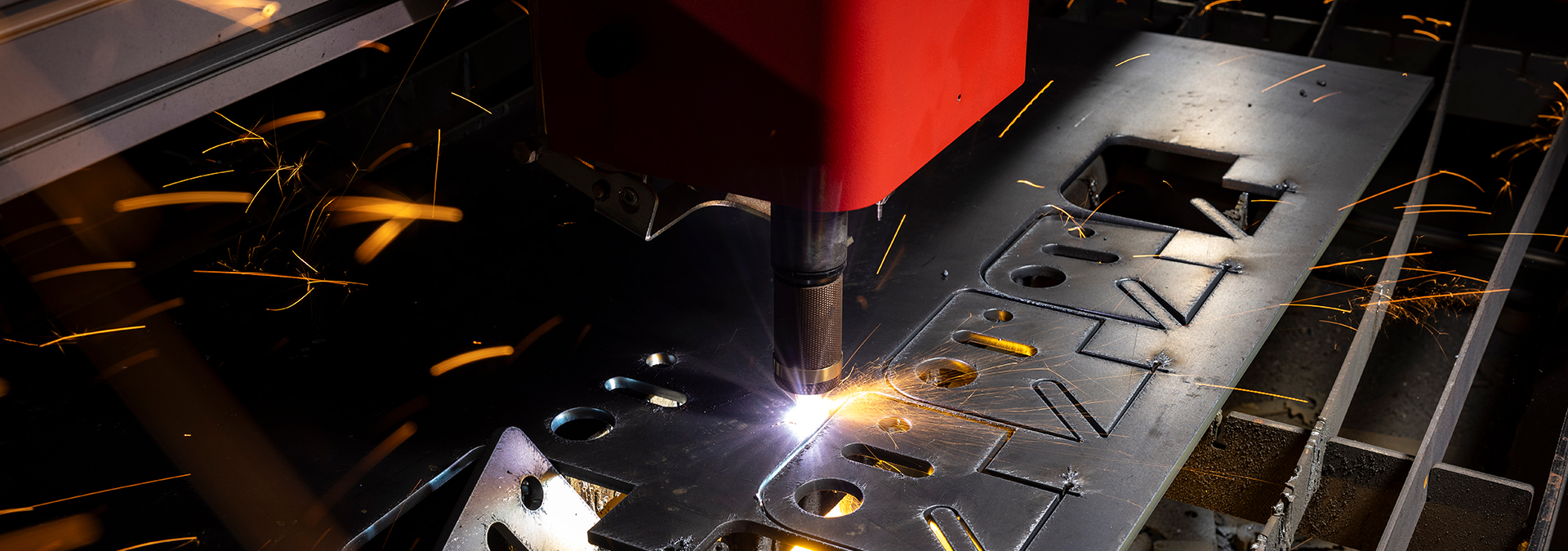
Why Choose Swift-Cut for Your CNC Plasma Cutting Needs?
At Swift-Cut, we understand the importance of precision, reliability, and cost-efficiency. Our range of CNC plasma cutting systems is designed to deliver exceptional tolerances, whether you’re working on small-scale projects or industrial applications. Here’s why Swift-Cut stands out:
- Advanced Technology: Our machines feature high-definition plasma systems for superior accuracy.
- User-Friendly Design: Easy-to-use software ensures operators can achieve tight tolerances without steep learning curves.
- Robust Support: We provide comprehensive training and support to help you optimize your cutting processes.
- Customisable Solutions: Tailor our systems to meet your unique needs, ensuring maximum value for your investment.
CNC plasma cutter tolerances play a pivotal role in ensuring precision and quality across various industries. By understanding the factors influencing tolerances and implementing best practices, you can achieve consistent, high-quality results while optimising costs.
Ready to take your metal fabrication capabilities to the next level? Explore Swift-Cut’s cutting-edge CNC plasma cutters today and experience the perfect balance of precision and performance.
Elevate Your Cutting Game with CNC Plasma
Investing in a CNC plasma cutter is more than just upgrading your equipment—it’s a step toward enhanced efficiency, precision, and profitability. From reducing waste to enabling intricate designs, CNC plasma technology transforms the way businesses approach cutting tasks.
For those seeking the best in CNC plasma cutting, Swift-Cut offers unparalleled solutions that combine innovation, reliability, and support. Explore Swift-Cut’s range of plasma CNC machines today and discover how they can revolutionise your workshop.
Ready to achieve precise tolerances and elevate your metal fabrication projects? Discover Swift-Cut’s advanced CNC plasma cutters, designed to deliver accuracy, efficiency, and reliability.
- What is CNC plasma cutter tolerance
CNC plasma cutter tolerance refers to the degree of accuracy a plasma cutter can achieve, defined as the allowable deviation from the specified dimensions of a cut. For example, a tolerance of ±0.5mm means the cut can vary by 0.5mm above or below the desired size. - What is the typical tolerance for a CNC plasma cutter?
Typical tolerances for standard CNC plasma cutters range from ±0.5mm to ±1mm. High-definition plasma cutters can achieve tighter tolerances, as precise as ±0.25mm, depending on the material and machine settings. - How can I improve the tolerance on my CNC plasma cutter?
To improve tolerance, regularly maintain your machine, optimize settings like speed and amperage, use high-quality consumables, secure materials with proper fixturing, and perform test cuts to refine parameters. - What affects the accuracy of CNC plasma cutting?
Accuracy is affected by factors such as machine quality, material type and thickness, cutting speed, plasma gas settings, kerf width, and the operator’s skill level. - Can CNC plasma cutters achieve the same precision as laser cutters?
While CNC plasma cutters offer excellent precision, laser cutters can achieve tighter tolerances, often within ±0.1mm, making them ideal for intricate designs. However, plasma cutters are more cost-effective and versatile for thicker materials. - Is CNC plasma cutting suitable for thin materials?
Yes, CNC plasma cutters are suitable for thin materials, but extra care must be taken to prevent warping due to heat distortion. Slower cutting speeds and proper settings can improve results. - What industries need tight tolerances from CNC plasma cutters?
Industries such as automotive, aerospace, industrial manufacturing, and architectural fabrication require tight tolerances to ensure the quality and functionality of their components. - How does kerf width affect plasma cutter tolerances?
Kerf width is the material removed during cutting. Variations in kerf width can impact tolerances, as a wider or inconsistent kerf may cause deviations from the desired dimensions. - What’s the difference between standard and high-definition plasma cutters?
Standard plasma cutters are more cost-effective but offer looser tolerances (±0.5mm to ±1mm). High-definition plasma cutters provide tighter tolerances (as low as ±0.25mm), delivering more precise cuts with superior edge quality. - Why is CNC plasma cutting better for thicker materials?
CNC plasma cutting excels with thicker materials due to its ability to cut through them quickly and efficiently, offering a good balance of precision and cost compared to methods like laser cutting, which struggle with thicker metals.