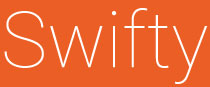
Welcome to the My-Swifty support section.
Swifty 610 technical FAQs
Browse our FAQs below and find the answers to your questions. If you can’t find the help you’re looking for here, you can use our online support system to submit your question to the Swifty team.
What do I do if my plasma will not fire?
First, check if the consumables are correctly fitted and if they are not, refit and try again.
If they are correctly fitted, make sure the work lead is securely connected to the table and the plasma. Also make sure the plasma connections are correctly fitted.
If the plasma still does not fire, please check which bar if air pressure you have connected to the plasma, it needs to be a 7-9 one. If it is the right one, make sure you turned ON the power on the plasma and then check if the torch fires when you press “Torch on” on the CNC screen. After this step, please check if you can move the machine around the table and if you can, make sure your PC is connected to the CNC, see question “Machine will not connect to my PC”.
What do I do if there is excessive fume created?
First, check if the table bed is filled with water to the correct level. If it isn’t please see question “My machine will not connect to my PC”. If it is, please check if the plate is contaminated with oil, paint or some chemical and if it is clean the plate or add extraction above the table
My Emergency-stop will not reset.
Check if the software is connected to the CNC. If it isn’t please see question “My machine will not connect to my PC”.
What do I do if my gantry twists?
Make sure the belts are secure below the covers.
Then make sure that all drive shafts are moving. If they are but one of the drivebelts has lost teeth, please contact support.
Machine will not connect to my PC.
Please make sure you followed the installation instructions.
Also, check your ethernet port settings.
My machine will not move
Please watch the operating video and home axes and make sure the X and Y axes are homed.
If this does not work, try closing and reopening the CNC software and then try to reconnect and home. If this worked, get cutting! If it didn’t, please contact support.
If after restarting the CNC software, the machine will still not home, please make sure you have set up your ethernet port and watched the set-up video/ manual.
My parts and table are starting to corrode
Make sure you are using the anti-corrosive additive in the waterbed. If you are, make sure the quantities added are correct. If the are not, top up the additive.
Why does the plasma torch rub on the plate?
First, check if the plate is flat. If it isn’t clean the slats and level the plate.
If it is clean, make sure the torch height set is using the height setting pieces and also that the 3-stage height control is working as the video shows.