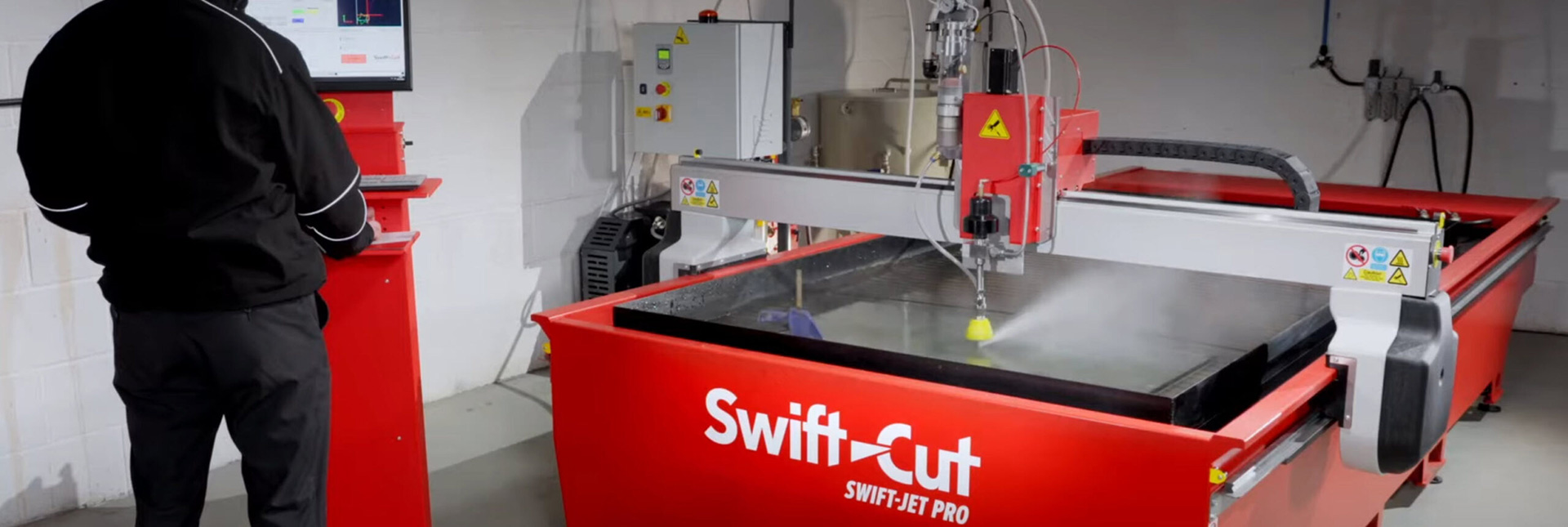
Unlock the Power of Waterjet cutting machines
How Waterjet Cutting Works Waterjet cutting machines utilise high-pressure water streams mixed with abrasives to cut through materials with precision. This technology allows for intricate designs and clean edges without heat distortion.
What you’ll learn about Waterjet Cutting
This guide covers everything you need to know about waterjet machines – from how they work to their cost-effectiveness and applications. Whether you’re in manufacturing, design, or construction, discover how this tool can transform your processes.
What is a Waterjet cutting machine?
In today’s competitive manufacturing world, precision and versatility are crucial. Enter the waterjet cutting machine – a powerhouse tool capable of delivering high-quality cuts across various materials without generating heat distortion. Whether you’re in aerospace, automotive, or art, waterjet cutting machines are proving to be essential for precise, reliable cutting. This guide explores how waterjet technology works, its advantages over traditional methods, and why it’s becoming an industry staple.
What is a Waterjet cutting machine?
A waterjet cutting machine is an advanced cutting tool that utilises a high-pressure jet of water, often mixed with abrasive substances like garnet, to slice through materials with pinpoint accuracy. Unlike traditional cutting methods that generate heat, a water cutting table uses the immense force of water to achieve clean cuts, making them ideal for delicate or heat-sensitive materials. This cold-cutting technique prevents warping, which is crucial in industries requiring exact tolerances, such as aerospace.
How Waterjet Cutting Works
Waterjet cutting operates by directing a high-velocity stream of water, reaching up to 60,000 PSI, at the material surface. When abrasives are introduced, this water stream can slice through dense materials such as metals, ceramics, and composites. The high pressure transforms water into a highly efficient cutting tool that can produce intricate designs and edges without compromising material integrity. By eliminating heat in the process, waterjet machines maintain the original properties of the materials they cut, allowing for applications where strength and precision are vital.
Just how significant is the impact of pressure? Check out this article which gives an informative and multi-faceted answer: An Engineer’s Guide to Waterjet Cutting – Engineering.com
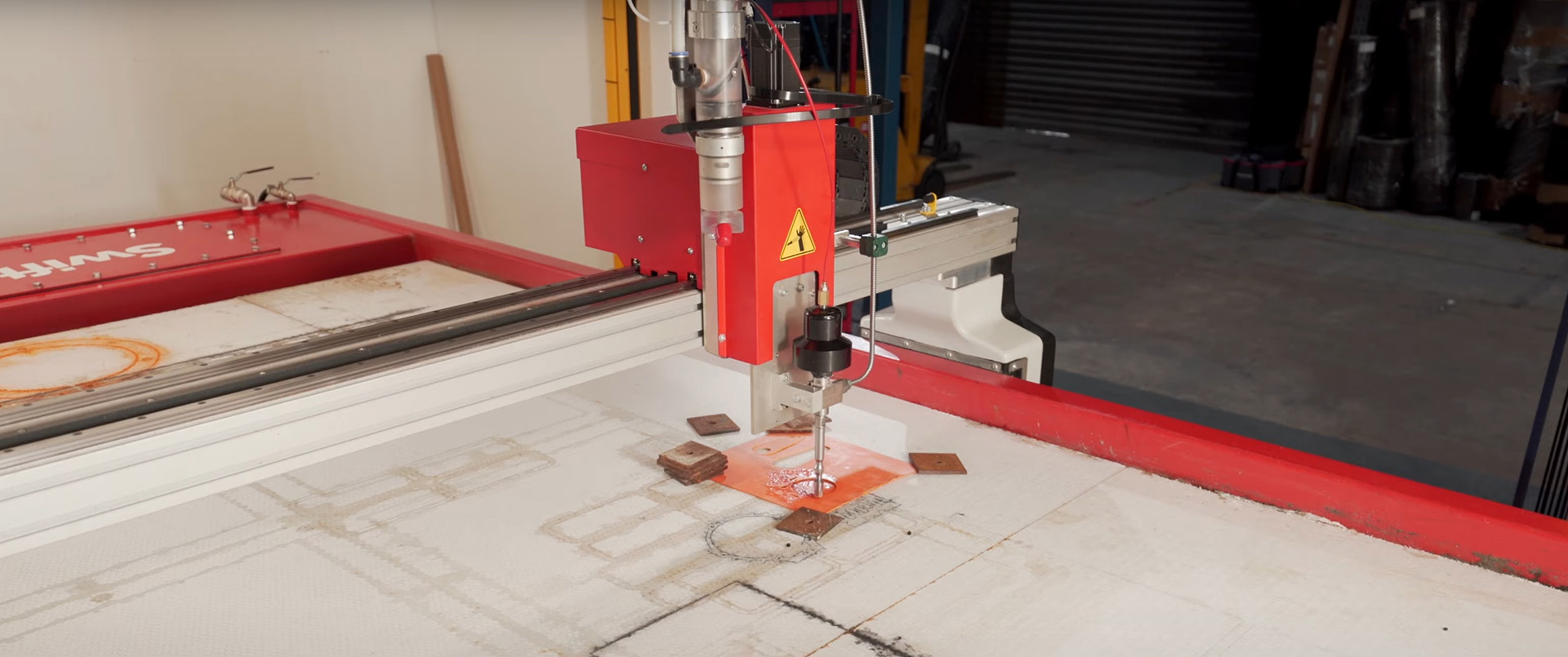
Applications Across Industries
Waterjet cutting machines are renowned for their versatility and precision, making them invaluable tools across a wide range of industries. Here’s a closer look at how different sectors leverage waterjet cutting technology:
Aerospace Industry: In the aerospace sector, waterjet cutting is crucial for fabricating complex components from high-strength materials like titanium and aluminium. These materials are often required to meet strict weight and durability standards. Waterjet cutting machines can cut intricate shapes with high precision, ensuring that parts fit together correctly without the need for secondary processes. Additionally, the cold-cutting nature of waterjet technology eliminates the risk of heat distortion, preserving the integrity of sensitive components.
Automotive Industry: Waterjet machines are widely used in automotive manufacturing for cutting components such as brackets, panels, and custom parts. The ability to handle a variety of materials, including metals and plastics, allows manufacturers to create lightweight, durable parts with complex geometries. Waterjet cutting also aids in prototyping, enabling designers to quickly produce and test new designs without extensive tooling.
Manufacturing and Fabrication: In general manufacturing and fabrication, waterjet cutting offers a flexible solution for producing a wide range of products. It can cut materials such as stainless steel, glass, stone, and even food items. This versatility makes waterjets suitable for applications ranging from kitchen countertops to intricate signage. The precision and cleanliness of waterjet cutting also reduce material waste, enhancing overall production efficiency.
Construction and Architecture: In the construction industry, waterjet cutting is employed for creating unique architectural elements, decorative facades, and custom stonework. The technology allows for intricate designs that can enhance aesthetic appeal while maintaining structural integrity. Waterjet cutting is also used in cutting tiles and other construction materials, ensuring clean edges and precise fits.
Art and Design: Artists and designers are increasingly turning to waterjet machines to create detailed sculptures and installations. The ability to cut complex shapes in materials like metal, glass, and stone enables artists to realize intricate designs that would be difficult or impossible to achieve with traditional tools. Waterjet cutting opens up new creative possibilities, allowing for unique and expressive works of art.
Marine Industry: In the marine sector, waterjet cutting is used for fabricating parts for boats and ships, such as hulls, decks, and interior components. The resistance to corrosion and ability to cut thick materials make waterjet cutting machines ideal for this environment. Additionally, the precision of waterjet cutting allows for the creation of complex shapes required in marine design.
Medical Equipment Manufacturing: Waterjet technology is also applied in the medical field for manufacturing surgical instruments and implants. The ability to cut delicate materials with precision ensures that medical devices meet strict quality standards while reducing the risk of contamination. Waterjet cutting can handle various biocompatible materials, making it suitable for a range of medical applications.
Energy Sector: In the energy industry, particularly in renewable energy, waterjet cutting is used for fabricating components for wind turbines and solar panels. The technology can efficiently cut through various materials, helping to produce parts that are both lightweight and strong, essential for the demands of energy generation.
Waterjet cutting machines have established themselves as essential tools across many industries, thanks to their versatility, precision, and ability to handle a wide range of materials. By understanding the diverse applications of waterjet cutting technology, businesses can leverage its benefits to improve their production processes and create high-quality products tailored to their specific needs.
Benefits of Waterjet Cutting
Waterjet cutting machines offer numerous benefits, making them a valuable addition to any workshop:
High Precision: Waterjet cutting allows for accuracy within thousandths of an inch, accommodating designs with intricate detailing. This precision is unmatched by many other cutting methods, allowing manufacturers to produce high-quality, customised parts.
Material Versatility: From soft materials like rubber to hard metals such as steel, waterjet machines are equipped to handle a variety of surfaces and densities. This broad adaptability saves costs on multiple cutting tools for different materials.
Environmentally Friendly: Unlike plasma or laser cutting, waterjet cutting machines produce no hazardous waste and minimise airborne particles. This aligns with green manufacturing standards and reduces environmental impact
No Heat-Affected Zones (HAZ): The absence of heat in waterjet cutting is a major advantage, especially for materials that may lose strength or deform under high temperatures. This also makes waterjet cutting machines suitable for materials that cannot be cut with lasers or plasma.
Cost-Effectiveness: By reducing material waste and speeding up production, waterjet cutting machines help lower costs, particularly in large-scale projects where precision and efficiency are key.
Waterjet Cutting vs. Traditional Cutting Methods
How does waterjet cutting compare to other common techniques like laser and plasma cutting? Let’s break down a few distinctions:
Laser Cutting: While laser cutting offers high precision, it’s limited to thinner materials and often leaves a heat-affected zone. Waterjets, by contrast, handle thicker materials without compromising their properties, making them more versatile.
Plasma Cutting: Plasma is efficient for metals but lacks the same level of accuracy and is often less suited for non-metals. Waterjets, on the other hand, can cut almost any material with fine detail, making them the superior choice for mixed material projects.
Traditional Cutting: Traditional cutting methods are limited by the type and thickness of materials they can handle. Waterjets allow for flexibility and precision that conventional methods cannot match, especially on complex projects.
Waterjet cutting machine Cost and Maintenance
When considering the investment in a waterjet machine, price is often a determining factor. While initial costs may be higher than some cutting alternatives, the longevity and versatility of a waterjet cutting machine make it a worthwhile investment. The Swift-Jet Pro waterjet cutting machine price varies based on specifications like pressure levels, cutting area, and whether it includes abrasive capabilities.
What is the Cost to Buy and Run a Waterjet cutting machine?
The purchase price of a waterjet cutting machine depends on the features, and level of automation, with machines starting from approximately £60,000 in the UK. Additionally, operational costs vary based on water (find your water supplier here) and electricity use and the cost of abrasive materials. Despite these costs, the reduction in waste and increased production speed mean waterjets often save money over time, particularly in high-volume manufacturing.
Cost and Investment Considerations: Waterjet Cutting Machine Price UK
While the waterjet cutting machine price may seem high initially, the technology’s efficiency and versatility often offset the cost over time. Waterjet cutting minimises material waste, speeds up production, and provides flexibility in handling a wide range of materials – all of which contribute to long-term savings and increased productivity. Additionally, operational costs, including water, electricity, and abrasives, should be factored into the total investment, though they remain competitive compared to other cutting methods like laser or plasma.
Customer Testimonials
Waterjet cutting machines have gained a loyal following from manufacturers to artists who appreciate the high-quality output and precision that only waterjet cutting machines can deliver. For instance, one Swift-Cut customer noted that switching to a waterjet cutting machine streamlined their process by reducing the need for multiple cutting tools. Another valued the machine’s ability to produce clean, intricate designs that traditional methods couldn’t achieve.
For a deeper look, case studies on our ‘How to choose’ section of Swift-Cut’s website explore real-world applications and customer success stories, showcasing how waterjet cutting machines are making a difference across sectors.
Whether you’re looking to enhance efficiency, cut down on waste, or bring your designs to life with precision, a water cutting machine could be the right investment for your business.
Contact us today for a quote tailored to your specific needs and discover how a waterjet cutting machine can transform your manufacturing process.
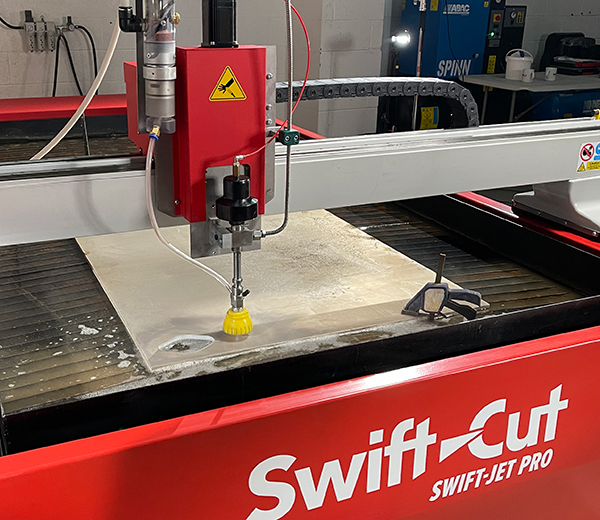
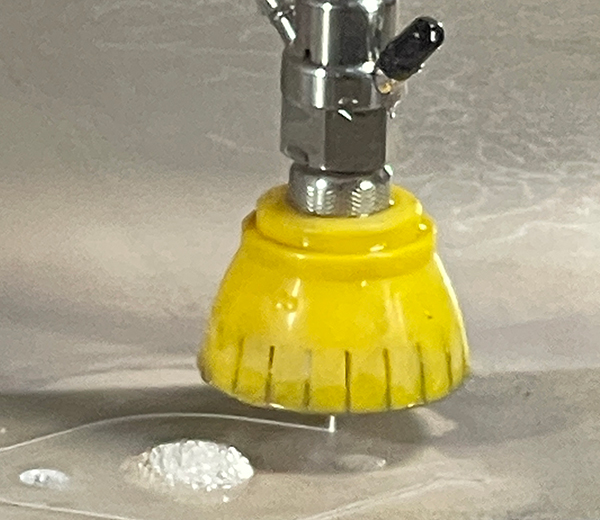
- What is CNC waterjet cutting, and how does it work?
CNC waterjet cutting uses a high-pressure jet of water, often mixed with abrasive materials, to cut through various materials with precision. A computer controls the jet’s movement to create intricate designs. - What materials can a CNC waterjet machine cut?
CNC waterjet machines can cut a wide range of materials, including metals, glass, stone, ceramics, composites, and plastics, without altering their structural integrity. - Why is CNC waterjet cutting better than laser or plasma cutting?
CNC waterjet cutting offers superior versatility, can cut non-conductive materials, doesn’t produce heat-affected zones, and delivers clean edges without additional finishing. - How accurate are CNC waterjet cutters for detailed designs?
CNC waterjet cutters are highly accurate, with tolerances as tight as ±0.003 inches, making them ideal for detailed and intricate designs. - Which industries use CNC waterjet cutting the most?
Industries like aerospace, automotive, construction, metal fabrication, and art rely heavily on CNC waterjet cutting for its precision and material versatility.
- How much does a CNC waterjet cutting machine cost?
The cost of a CNC waterjet machine varies based on size, features, and capabilities, ranging from £60,000 to over £250,000. - Is CNC waterjet cutting environmentally friendly?
Yes, CNC waterjet cutting is environmentally friendly as it doesn’t produce hazardous fumes or heat and uses recyclable materials like water and abrasives. - What are the maintenance costs for CNC waterjet cutting machines?
Maintenance costs depend on machine usage and components but typically include replacing nozzles, pumps, and seals. Regular servicing ensures optimal performance. - Can CNC waterjet cutting handle thick materials like metal or stone?
Yes, CNC waterjet machines can cut through thick materials, including metals over 12 inches and stone up to 10 inches, with excellent precision. - Where can I find CNC waterjet cutting services near me?
You can find reliable CNC waterjet cutting services through local manufacturing shops or by contacting Swift-Cut for recommendations or equipment purchases.