Advantages and Disadvantages of a downdraft table versus a water table
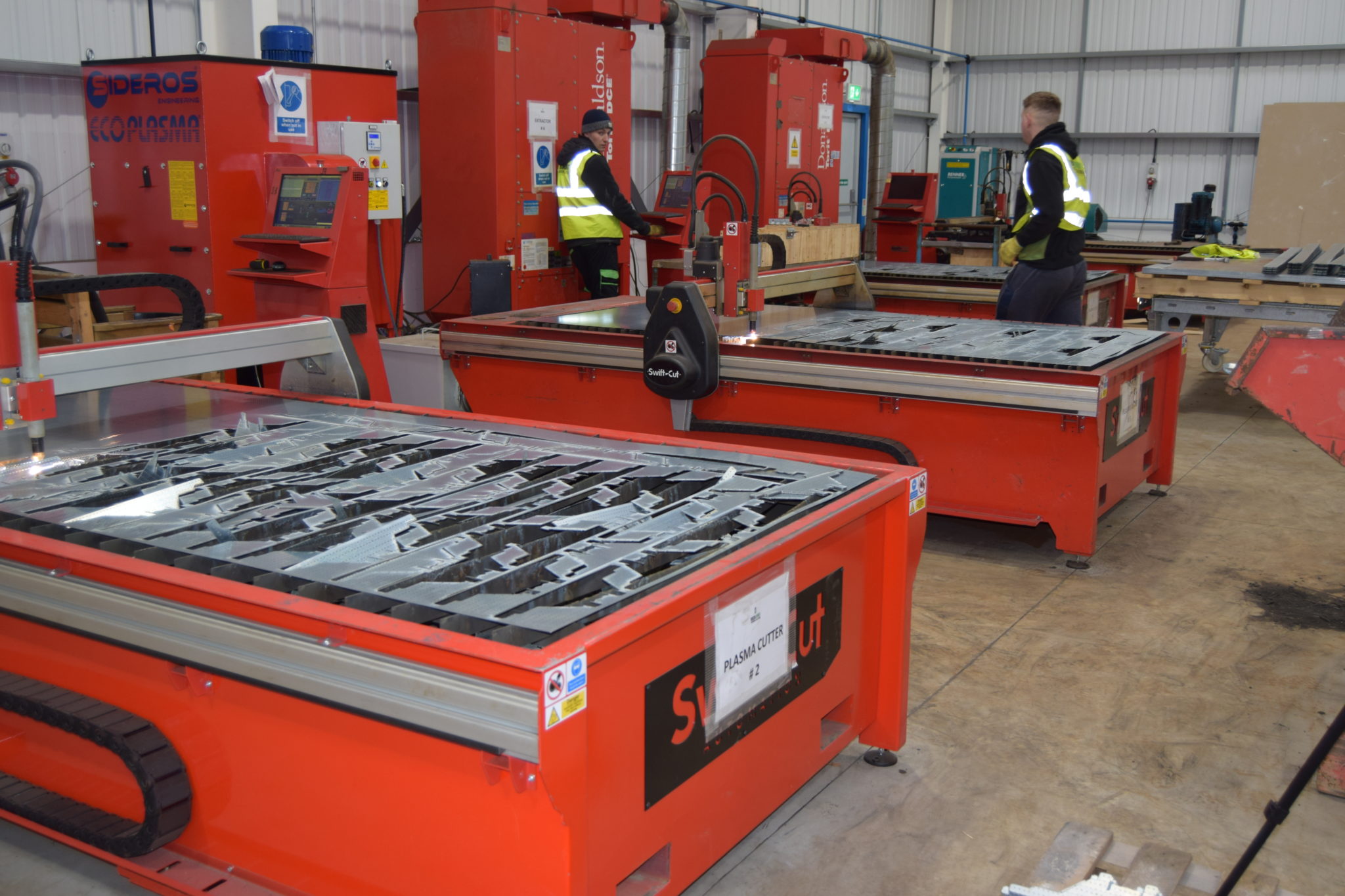
Downdraft Table advantages:
- Straight forward maintenance once set up with no water levels to check or refill
- Any fume created is drawn down and away from the operator, even when cutting material that isn’t positioned flat on the slats (i.e. box section, I beam etc.)
- Dust is usually collected in a drum or hopper for easy disposal – there’s no pumping, no sludge, and no figuring out how to dispose of contaminated water.
- Maintenance time is minimal compared to a water table. The dust collector will require filter changes, but this is carried out quickly and cleanly meaning less down-time for the plasma compared to emptying, scrapping and refilling a water table.
- Cut parts are ready to be used straight from the table with no time wasted having to dry things off.
- A downdraft table removes virtually all fume and particulate and as it’s a dry process there’s no splashing of water, which can create a slip hazard.
- A zoned downdraft table (optional on the Swift-Cut Pro and XP series) collects fumes and dust only where they are being produced and keeps all fumes contained to a small area, meaning the extraction fan or unit can be much smaller and economical compared to on open downdraft table.
Downdraft Table disadvantages:
- More expensive to purchase than a water table – the cutting bed generally costs more, and you will need to purchase an extraction fan or filtration unit, as well as additional ducting.
- Depending on your business location, you may have to filter the air before it exits the building – filters can be expensive and will require changing once or twice a year.
- If you are wanting to avoid expensive filtration systems, the table will need to be sited near to an outside wall, which could be limiting in some building layouts.
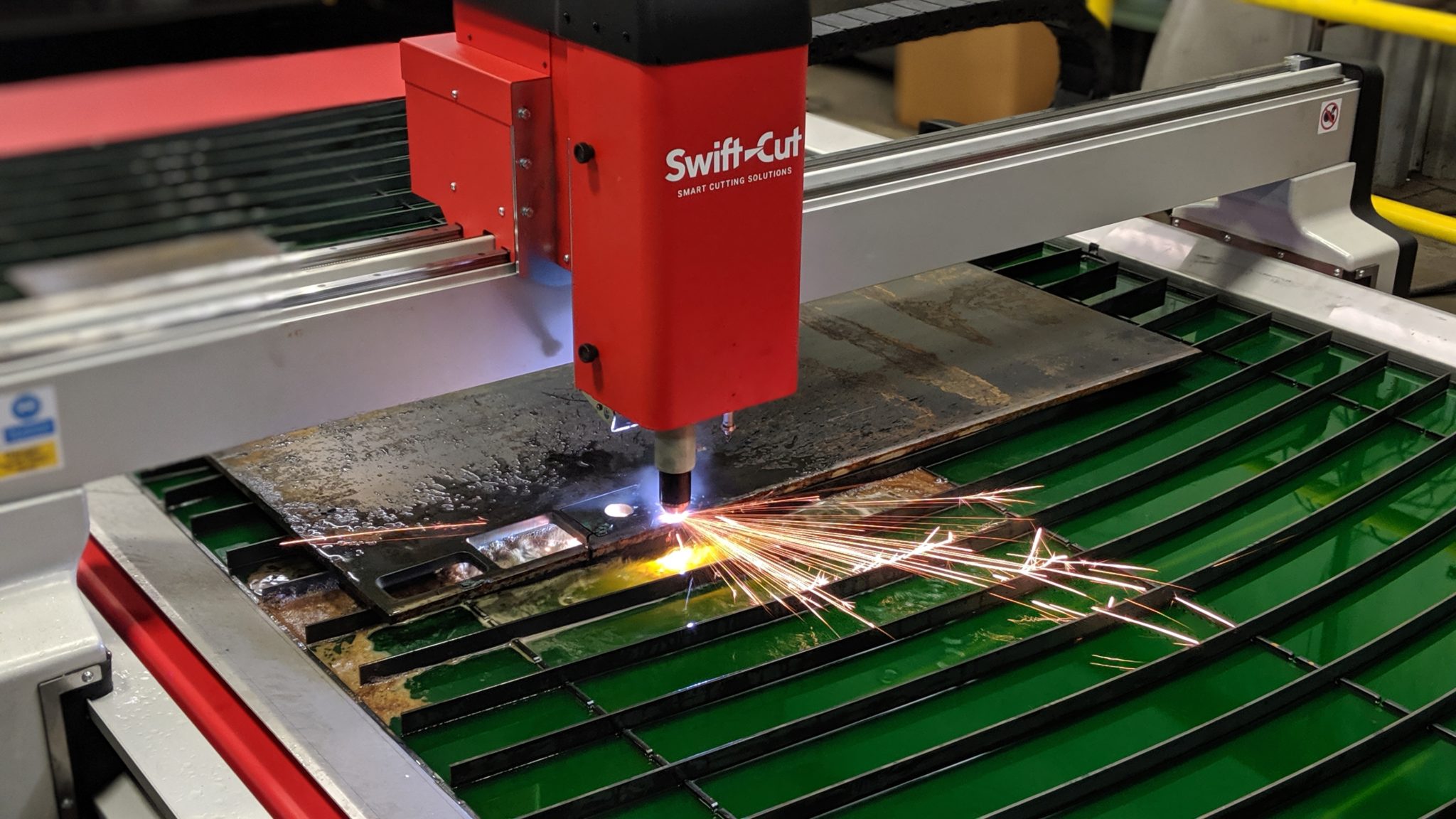
Water Table advantages:
- Less expensive than a down-draft table to purchase and ongoing running costs can be cheaper (i.e. water is cheaper than electricity)
- Will not require a dust collector in most areas.
- Reduces noise – a filtration system or extraction fan can significantly increase the overall noise levels of the table when cutting.
- Reduces heat distortion and keeps parts cooler and this can be beneficial on thinner materials where warping is more of an issue. Parts are cooler to the touch which makes them easy to remove and use immediately.
- Better edge metallurgy on some stainless-steel parts.
Water Table Disadvantages:
- Rust will get on slats, plate and machine components.
- Increased edge roughness and dross if water splashes onto the part being cut.
- Less productive as slower cutting speeds are needed.
- Difficult to clean table, especially as time goes on without any maintenance.
- Water in unheated shops or cold areas will freeze.
- The water needs to be treated regularly with an anti-rust and anti-fungal additive to avoid it becoming a health hazard.
- Cutting certain grades of aluminium on a water table can offer a significant safety risk. Plasma + Aluminium + Water = Hydrogen Explosion Hazard.