Sanindus, in Mortsel is a piping company that designs, builds, supplies and installs piping systems, specialising in industrial pipelines made of steel, stainless steel and plastic. The company, which was founded in 1995, is active in sectors such as water purification, skid construction, production pipes, compressed air installations, dredging pipes and ventilation.
Fed up with waiting on long lead times from external suppliers, where waiting anything from five to fifteen days to have pieces cut was standard, Sanindus were keen to bring metal cutting work in-house and started to investigate methods, quickly realising that purchasing a plasma cutting machine would make it possible to respond more efficiently to their customer.
When a large oil tank project presented itself in early 2020, they decided it was time to commit and Wouters Cutting and Welding introduced them to the Swift-Cut Pro 3000 with a Hypertherm Powermax 105, capable of cutting to a thickness of 20mm.
‘There was a lot of cutting involved, which is why it was decided to proceed with the investment’
Raf Van Leuven, Project Leader.
Purely by chance, the project leader discovered even more uses for their Swift-Cut Pro 3000 table. They now use it for the processing of plastic, especially HDPE, which was always done by hand and was incredibly laborious and time-consuming. The drawing is now loaded onto the software and the engraving pen simply marks the position of the holes. The plastic is then removed and the holes drilled out manually.
That is the beauty of Swift-Cut, its innovative functions allow customers to use the machine in more ways than they ever imagined, making it an investment that often pays off in more ways than one.
After over a year, Van Leuvan said,
‘We have simply brought flexibility in-house. If we are on location and we come across unexpected things, we can make a drawing the same day and cut out the pieces. In the past, you sometimes ordered standardized pieces in the knowledge that you still had to adjust them on site, so as not to have to wait for delivery.’
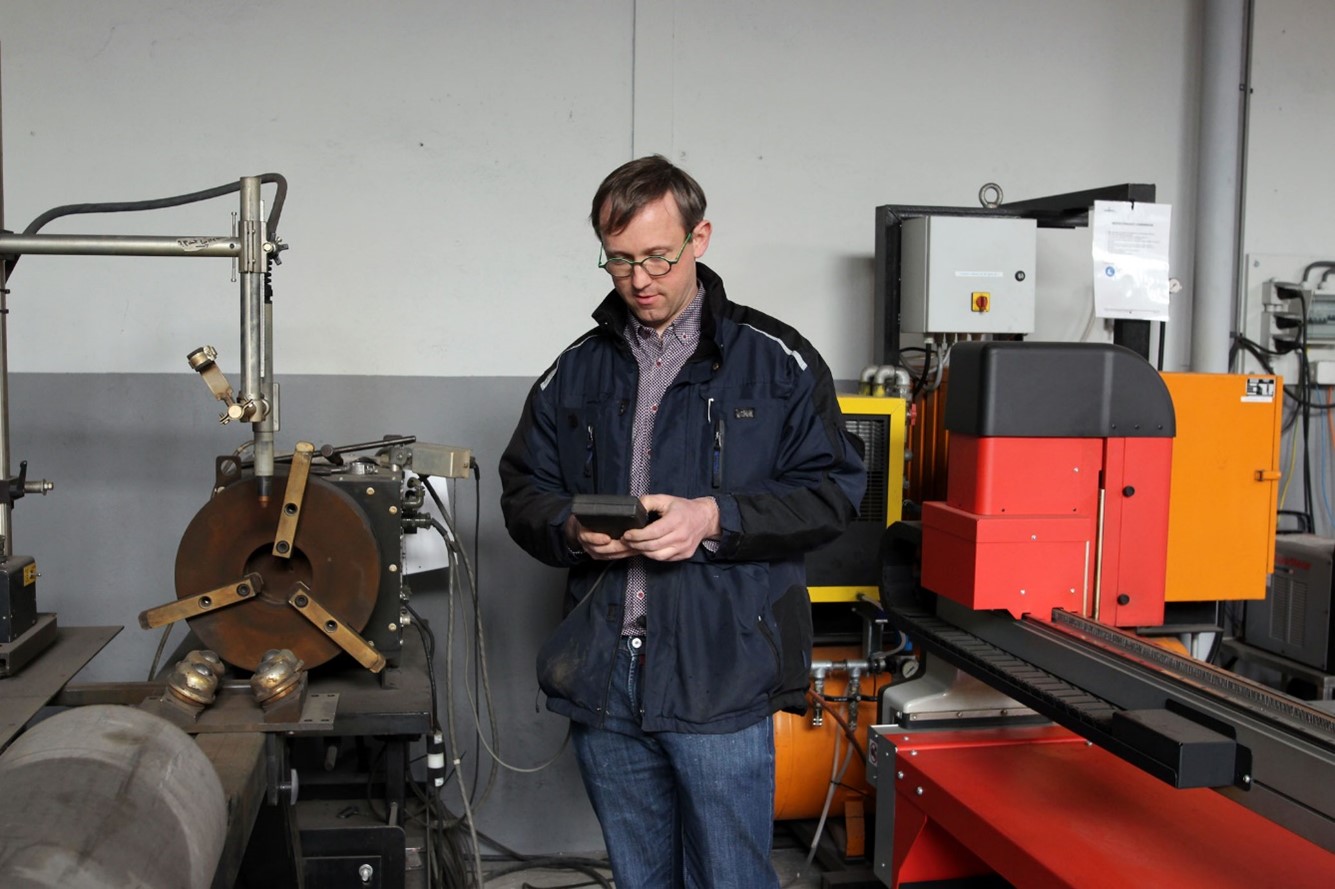
The Swift-cut plasma cutting machine is located with a Bugo machine so that both can share the same source. (Photo: Jerom Rozendaal)
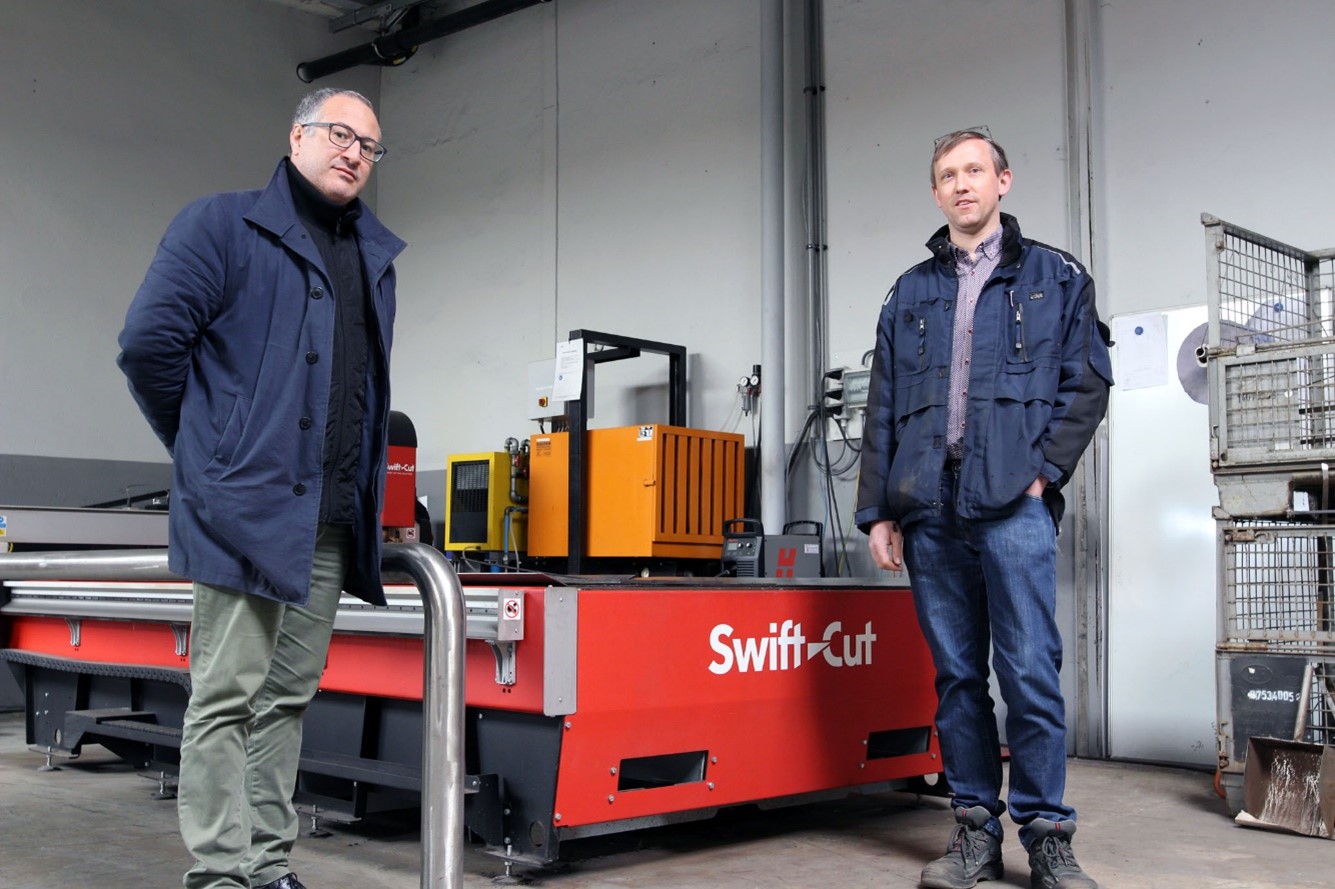
Raf Van Leuven, project leader at Sanindus and Rached Taheri of Wouters Cutting & Welding